Kinsley Pavilion Philadelphia, Pa
Michael Walsh
Construction Management
General Building Data
-
Building name (Kinsley Pavilion)
-
Location and site (Philadelphia)
-
Building Occupant Name (Confidential)
-
Occupancy or function types Hospital (Medical)
-
Size 203,000 SqFt
-
Number of stories above grade and total levels Basement +5 (74’ above grade)
Project Manager
General Contractor

Architects
Geotechnical
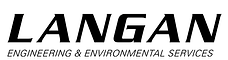
MEP/FP
Structural
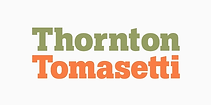
Architecture
-
Architecture (design and functional components)
-
The New pavilion will be taking the place of an earlier building previously located in the area. It will house 12 operating rooms, as well as 72 new patient rooms.
-
-
Major national model code/s
-
Chapters 2 through 29 and 31 through 35 of the International Building Code 2003, including Appendices C, E, G, H and I.
-
ICC Electrical Code 2003
-
-
Zoning Currently unavailable
-
Historical requirements of building or historical district where built NA
Building Enclosure
This section is to include very specific details about the various types of enclosure systems including windows, curtain wall systems (including the type of glass / glazing), facade / exterior wall materials and extents, and roofing. Note that Roofing is not the same as Roof. Roof generally refers to the structural framing and slab / decking used and is covered in the structural section. Roofing is the type of weather resistant covering used as part of the exterior enclosure (standing seam metal, EPDM, etc.). Shading devices may be described here or as part of the architecture description as they are often aesthetic as well. Photographs or renderings showing the facades or close up views of the enclosure elements often can save a lot of descriptive writing in this section. At a minimum use the two subtopics:
Sustainability Features
Included in this section should be a description and photos as appropriate of the major active and passive sustainability features of the building or site. Roof top gardens, green roofs (remember they have Roofing underneath…see previous section), solar shades, natural ventilations etc.
The building is going for LEED Silver. I am still in the process of obtaining the sustainability measures they are implementing in order to reach LEED Silver. The demolition of the previous building was done using LEED requirements.
Building Statistics Part II
Primary Engineering Systems
Demolition
The Kinsey Pavilion will be taking the place of two existing buildings that were demolished the summer. Demolition was done in two parts, interior and exterior. The reasoning for this is that the owner of the project is seeking LEED Silver. LEED awards points for things like salvaging old building materials and reusing them. In this case items such as casework, doors, frames, hardware, and skylights were removed carefully in order to ensure that they could be reused. The exterior demolition was done using cranes equipped with grapple claws. The material was then trucked offsite, crushed, and brought back to use as backfill material. In order to contain dust during the demolition, the site was constantly watered down to prevent any particles from becoming airborne. Also, in order to accommodate the new building utilities and an existing substation had to be relocated.
Construction
The primary building façade for this building is a face brick veneer on either steel studs or CMU’s. Other portions consist of manufactured stone or an insulated metal panel system on steel studs. The entire South side of the building, as well as the stair towers are designed using an aluminum storefront system. Other envelope features include a canopy system over the main entrance consisting of structural glass, as well as a green roof located at the grand lobby.
The roof of Kinsey pavilion is covered by an elastomeric roofing membrane. The top layer of the membrane is an air/vapor barrier will insulation, both will end up being tied into the structural metal deck. Flashing is included between roofing connections and areas such as where plumbing vents and pipes penetrate through the roof. Also located on top of the roof is a 40,000 gallon water tank for fire protection.
Electrical
The main electrical work for this project was in upgrading the hospital’s existing multi-phase electrical infrastructure. This was done by replacing the original 4160V service with new 13.2kV - 480/277 service. Other upgrades included installing a new generator, new electrical gear, new emergency and normal switch gears, and 13 new ATS switches. All of this work had to be planned out carefully so that it could be done in phases because the hospital must remain fully operational throughout the course of construction work. Each phase of the project required temporary facilities to be built in various locations. This required a lot of planning electrically because power needed to be supplied to each facility. Furthermore, hospitals require multiple redundancies built in to ensure the building will never be without power. These safety features greatly increase cost because they require the installation of many sensors and other devices.
Lighting
The lighting system for the Kinsley Pavilion consist mainly of LED strip lights and 4" fluorescent down lights. All of the room in the hospital have occupancy sensors in order to cut down on lighting needs in order to get LEED points. The operating rooms have many fluorescent lights in order to give surgeons as much task lighting as possible Large windows and numerous ceiling glass areas work to get the most natural daylighting as possible.
Mechanical
All of the mechanical equipment for the Kinsey Pavilion is divided up between the basement and fourth floor levels. Located in the basement are 14 AHU units, and 2 heat exchangers located in a larger mechanical room. The fourth floor houses an additional 6 AHU units, 8 pumps, 13 fans, and a rotary energy recovery wheel. From these two floors all of risers and branch ductwork distributes air throughout the building. Also incorporated into the mechanical system are a series of outdoor air louvers to take advantage of fresh air intake. Other devices included in the building to maximize efficiency are high/low duct pressure sensors. These sensors work to detect when too much air is flowing which leads to losses from leakage as well as disruptive loud noise, as well as detect when not enough air is flowing which could cause health problems.
Structural
This structure of this building was designed to utilize a steel frame, composite floors, and a steel deck roof. Columns and other structural steel elements for this project were over-designed because the hospital is planning on adding an additional three stories to the building in the future. Overall five crane locations will be used throughout the course of the project. After installing the super structure spray fireproofing will be applied to all members.